
Introduction
Nowadays tower cranes are complex and sophisticated installations. Modern tower cranes are equipped with electronic systems and are software controlled. For instance, cameras for ‘blind lifting’ are installed, safety devices to prevent load moment exceedance, as well as collision warning systems. The load moment, or torque, is the combination of the horizontal distance from the load to the mast – the outreach and the weight of the load. While exceeding the permitted torque, a warning will be issued, and the device will automatically switch off all crane movements, including the trolley. Due to these safety devices, the frequency of past accident scenarios like ‘crane instability', 'jib instability’ and ‘hoisting equipment instability’ is relatively low. ‘Load instability’ however is still a dominant accident scenario in crane accidents [1-3]. This makes tower cranes a critical, and inherent dangerous component on construction sites [4, 5]. Strangely enough there is little attention in scientific literature on causes of crane accidents how to prevent them [6-8].
Often, operator errors are seen as the main cause of crane accident. These installations, however are robust and crane drivers are professionals. Hoisting is a risky activity, frequently conducted under time pressure due to time and financial restrictions posed by construction management [9-12]. A few years ago, a tower crane collapsed in Rotterdam, seemingly without any cause. The Dutch Safety Board [13] investigated this accident, guided by the following research questions;
- What were the circumstances of the collapse of the tower crane?
- Which scenarios contributed to the collapse of the crane?
- Could other safeguards compensate for shortcomings in design or production?
- Could the Rotterdam crane accident be classified as a socalled ‘normal accident’?
Methodology
One of the metaphors used to understand accidents is the bowtie (figure 1). This bowtie gives a further refinement of the well-known Swiss cheese metaphor, and is a linear presentation of accident causation with more details on managerial influences [14, 15]. The centre of the bowtie is the so-called 'central event', a condition where one or more hazards (energies) are becoming uncontrollable. Accident scenarios are the arrows between hazard and central event, and from central event to consequences. These scenarios represent conditions whereby (a) hazard(s) is/are becoming risks, leading to effects like damage to properties, and/or accidents. The blocks within the arrows are barriers. These are physical entities that may stop, or reduce the flow of energy to and from the central event.
Figure 1 The Bow metaphor
Frequently scenarios left of the central event may develop over a considerable timespan, which may take years to reach a condition of an uncontrollable energy. Once this condition is present, scenarios leading to consequences, on the right side of the central event will develop far more rapidly, in matter of minutes, seconds of even shorter.
The bowtie also shows the relation to safety management, pictured in arrows going upwards. Management has the responsibility to identify, scenarios and central events, for the selection and identification of barriers, and for activities to ensure and optimize the quality of barriers, such maintenance, inspection, training for use and for rules for conflicts between safety and other business objectives. Other than the barrier choice, these management factors will have no direct effect on scenarios, but they will determine the effectiveness of the barriers [16].
The first two research questions are considering circumstances, causes and possible design faults of the crane accident. Answers to these questions refer to the left side of the bowtie, and form the basis for any accident investigation. When hazards, scenarios, and barrier failures are known, the investigation can address the organisational, and managerial context of the accident. For these two research questions the central event studied by the Dutch Safety Board was the instability of the crane. Three scenarios on the left side of the central event were considered 1) an exceedance of operational parameters, 2) failure of the tower construction, caused by weaknesses in the construction, and 3) an overload of the job. The first scenario involved a check on electronic components, the data carrier, and the crane’s electronic compatibility. This involved possible influences of electromagnetic fields on the data flow for crane movement control. The second scenario implied destructive materials research on the crane construction. And the third scenario related to an uncontrolled trolley movement, which can lead to the central event of load instability.
For the third research question, the European product and social guidelines for tower cranes were examined, as well as Dutch national legislation and crane inspection regimes. The last research question refers to Charles Perrow [17], who gave a sociological explanation for accidents in complex technological systems. According to Perrow, un-expected failures were built into these systems, making them inevitable. Such failures might appear trivial at the start of the accident process, but will cascade through the system in unpredictable ways, causing large events and dramatically reduce the safety envelope of the system, resulting in severe consequences. Complex systems, like production processes, with system determinants as interactive complexity and tight coupling, fulfil system conditions where these normal accidents will occur.
Result 1, circumstances of the accident
The trolley tower crane was peak less, meaning there was no top jib trolley tower crane, and the crane drivers’ cabin is the highest point of the crane (figure 2). Peak less cranes are easier to transport than other tower cranes. Because of the absence of a top jib, and these cranes are often used in construction projects with height restrictions, or on building sites with more than one crane in close proximity. The crane was installed at a 24 story high rise at a Rotterdam construction project. It’s hook height was 59 meters, and its mast was extended to a height of 96m. The crane was approved by an accredited inspection body.
Figure 2 Peak less crane at Rotterdam’ project
A 7-ton balcony slab was hoisted on the day of the accident. Together with the balancing device, the total load was 12.8t. Weather conditions were good. At first the crane driver hoisted the load around the building. The load moment protection device stopped the trolley movement, and the crane driver was hoisted over the building. Almost in place, workers on the balcony warned the crane driver not to move the load outwards but inwards. In reply the driver denied hoisting outwards. At that moment, the outreach was 27ms. Workers on the balcony saw the load sway away, and shortly afterwards the crane collapsed. The crane driver died after a fall of 40m. The devastation was great.
Result 2, scenario analysis
For the first scenario, the adjustment of the load protection device was critical. The Safety Board assumed the device was turned on because it prevented hoisting the load around the building. The maximum load weight of the crane was 16t, outreach 23m, and 13t at an outreach of 28m. With a load protection device switched off or failed, the crane would collapse when exceeding these load moments. Observations by researchers of the Board soon after the accident confirmed the assumption of the device being switched on. But with a total load of 12.8t at an outreach of 27m, the crane was hoisting against the limits of its maximum load torque.
The second scenario refers to material defects. The mast was bent, broken and wrenched apart. The steel structure was build following design specifications, as the chemical analysis showed. But the surface of the fracture was fibrous in structure, pointing at a so-called ‘tough break’ (figure 3). These type of breaks were indications for a structural overload, and not for material defects.
Figure 3 Deformations, and tough breaks
The last scenario deals with jib overload. A load can swing, due to clashes against objects, or caused by a gust of wind. These conditions were not present during hoisting. The weather was calm, and no collisions were reported. A trolley out of control, caused by control malfunctioning, or excessive jib bending, can also cause jib overload. The starting position of the hoist, when the load almost reached the balcony, was almost static. An incorrect command from the crane driver could have caused malfunctioning of the crane. An outward trolley command of the crane driver was not very likely, regarding the communication between the driver and workers at the balcony. Another option was an electromagnetic interference of the crane control cables. This may have caused a failure of the trolley movement. Interference could be induced by the motors’ power cables, or the antenna of the gsm, the global system for mobile communication. This antenna was installed in the crane switch box. It was observed that these power, and data cables were bundled together over a distance of 20m along the back jib. So there could have been an impact on data transport, and during a test this impact was detected. But these events would lead to an error message, and would stop the trolley transport. A final option would be an excessive jib bending. According to the manufacturer the maximum sag of the jib was 1° below horizontal. During a simulation the jib bent 2.1° below level with a 13t load and an outreach of 27m. These measurements were taken with a static load. If the load would swing, or the hoist cable would come to an abrupt stop, the bend is greater. If the trolley moved out to a 50m radius, the calculated bend is 5.6° below level. This means the flexibility of the crane exceeded the values calculated by the manufacturer, having an impact on the trolley movements. These movements are controlled by the trolley motor. If the motor is accessed, the settings determine the time needed for maximum power (magnetisation time), and the release of the trolley breaks (break time). The electrical motor works using a spool, which has to magnetise before it can deliver power. Observations at the collapsed crane showed the brake time was set on 0 sec, together with a short magnetising time. As a consequence the motor was not at full power yet, while the breaks would have be released once the motor was started. Giving the extensive bending of the jib, the trolley and the load was running out of control down the sagged jib.
Result 3, other safeguards
The manufacturer, actors around the building site and related to management and maintenance of the crane, they were parties involved during the lifetime of the collapsed crane. The German manufacturer was the first party. The manufacturer was assembling the crane, using outside expertise for the design, calculations, and the production of electrical components. Outsourcing will create a problem when elements are supplied by different venders and need to be assembled in a complex structure like a crane. Necessary expertise should be in place to supervise this assembly process to secure effects on its structure and functionality. Before putting the crane on the market the manufacturer has to comply with the European Machinery Directives, the Electromagnetic Compatibility Directives and the directives relating to low voltage and noise emission. A manufacturer will need to document compliance with these directives in a so-called EC declaration of conformity and in a Technical Construction File. With this documentation the crane can be provided with a CE mark (Conformité Européenne), implying the crane does not require further tests on matters of quality and safety by an external approval authority in European countries. A manufacturer may himself declare his product is complying with European product directives. The collapsed crane was provided with a CE mark, only its documentation could not be tracked.
The second group were the contractor(s), the developer and the municipality. By law a building site requires a health and safety plan; a risk inventory and evaluation. The plan is reviewed by the municipality’s Building Control department and the department then goes onto monitor compliance.
The third group of actors involved in the management and maintenance of the crane, are the crane owner, the management foundation of certification schemes, the Vertical Transport Certification Board of the Netherlands (TCVT) and the Labour Inspectorate. The TCVT inspection schedule deals with the quality of construction after the tower crane has been installed, the checking of the certificates for the crane cables used and the testing of the load moment protection device. The collapsed crane passed inspection without a hitch. Error messages, risks regarding the functionality of the crane, the focus on intermediate maintenance and the risks attached to new and complex electronic and computerised crane control systems are not addressed during these inspections.
The last party, the Labour Inspectorate, monitors the compliance with laws and with the regulations for maintenance and inspection, the requirements made of crane operators, the hoisting regulations and compliance with health and safety plans. The test results are then registered in the crane log book.
Result 4, normal accident
Perrows’ normal accidents derive from complex and tightly coupled production systems, and a crane and its hoisting activities are not directly a production system. But the high masses involved, the height of operation, and the quality of the controls transformed the safety envelope of the crane. Combined with an over-bending of the jib, the crane system has similar characteristics as these production systems. The dynamics of the system are poorly understood, processes like data transport interference, consequences of control settings, and intrinsically poorly monitored and instrumented processes resulted in a very limited failure recovery time, and critically narrow limits of safety. There were no time-buffers or redundancies.
Discussion and conclusion
The conditions of the fatal hoisting activity were good, weather conditions were fine, and no collisions with the load and other objects were present. Just before the crane collapse, the hoisting conditions were static, making the collapse of the crane at first a so-called impossible accident. The analysis of the Dutch Safety Board however did show specific risks and accident scenarios of these tower cranes. The circumstances and the scenarios leading to the central event ‘load instability’ were clear. An excessive bending of the jib, combined with inadequate control settings created an uncontrolled movement of the trolley, running along the jib, and exceeding the maximum load moment. These dynamic forces resulted in the crane collapse, and are the leading indicators of this accident. The excessive bending was not predicted by the manufacturer and the accident was classified as a 'normal accident' [17]. It was a fault in the design of the crane. This is the answer to the first, the second and the fourth research question.
For the third research question the research concluded the crane was provided with a CE-mark, giving the impression the crane was safe. But structural scenarios like jib bending was not part of the CE qualification. Also the inspections and supervisions by the Factory Inspectorate, the certification board (TCVT) and the municipality did not address structural and operational scenarios. This finding corresponds with findings in other fields on the inefficiency of supervision to deal with leading accident indicators [18]. Once on the market there appears to be no further effective safety net for the detection of structural and operational weaknesses.
Finally one question remained after the analysis of the crane accident, the question of the selection of a peak less crane. A top jib crane will have a more ridged jib. Arguments in favour of a peak-free crane were not present at the Rotterdam construction site. There was no height restriction, and no other cranes in sight. Unfortunately the accident analysis could not provide an answer to this question.
References
- 1. Beaver J, Moore J, Rinehart R Schriver W (2006). Crane related fatalities in the construction industry. Journal of Construction Engineering and Management 132(9):901910
- 2. Paas C, Swuste P (2006). Mobile cranes, what goes wrong? A survey on dominant accident scenarios. Journal of Applied Sciences 19(3):4755 (in Dutch)
- 3. Tam V, Fung I (2011). Tower crane safety in the construction industry: a Hong Kong study. Safety Science 49:208215
- 4. Parfitt M (2009). Cranes, structures under Construction, and temporary facilities: are we doing enough to ensure they are safe? Journal of Architectural Engineering, March 12 periodical on structural design in construction. May p. 6773
- 5. Sertyesilisik B, Tunstall A, McLouglin J (2010). An investigation of lifting operations on UK construction sites. Safety Science 48:7279
- 6. Swuste P (2005). Safety Analysis vertical transport mobile cranes. Safety Science Group, Delft University of Technology (in Dutch)
- 7. Swuste P (2013). A normal accident with a tower crane. Safety Science 57:276282
- 8. Shapira A, Lyachin B (2009). Identification and analysis of factors affecting safety on construction sites with tower cranes. Journal of Construction Engineering and Management 135(1):2433
- 9. Schexnayder C (2003). Crane accidents construction sessions, roebling award, books, conferences. Practical
- 10. Aneziris O, Papazouglou I, Mud M, Damen M, Kuiper J, Baksteen H, Ale B, Bellamy L, Hale A, Bloemhoff A, Post J, Oh J (2008). Towards risk assessment for crane activities. Safety Science 46:872884
- 11. McDonald B, Ross B Carnahan R (2011). The Bellevue crane disaster. Engineering Failure Analysis 18:16211636
- 12. Swuste P Frijters A Guldenmund F (2012). Is it possible to influence safety in the building sector? A literature review extending from 1980 until the present. Safety Science 50:13331343
- 13. OVV, De Onderzoeksraad voor Veiligheid Dutch Safety Board (2009). Collapse of a tower crane Rotterdam July 10th 2008.
- 14. Visser K (1998). Developments in HSE Management in Oil and Gas Exploration and Production. In: Safety management, the challenge of change. Hale A Baram M (eds). Pergamon, Amsterdam, p 4366
- 15. Swuste P (2008).You will only see it if you understand it Human Factors and Ergonomics in Manufacturing, 18(4):438–453
- 16. Guldenmund F Hale A Goossens L Betten J Duijm N (2006). The development of an audit technique to assess the quality of safety barrier management. Journal of Hazardous Materials 2006:130:234241
- 17. Perrow C (1984). Normal accidents. Basic Books, New York. A reprint has been published in 1999: Perrow C (1999). Normal Accidents: living with highrisk technologies. Princeton University Press, Princeton, New Jersey
- 18. Jongen M Swuste P (2014). Does safety culture regulate process safety? Can safety culture be a credible indicator during supervision audit of process safety? (in Dutch). Journal of Applied Occupational sciences 27(1):in production
Papers relacionados

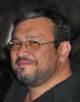

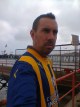
